Innovation Unleashed: The Future of CNC Machine Tools
Release time:
2025-01-14
Innovation Unleashed: The Future of CNC Machine Tools Table of Contents Introduction to CNC Machine Tools Historical Development of CNC Technology Current Landscape of CNC Machine Tools Technological Advancements Shaping the Future The Role of Automation in CNC Machining Sustainability in CNC Machining CNC Machine Tools and Industry 4.0 Challenges Facing CNC Ma
Innovation Unleashed: The Future of CNC Machine Tools
Table of Contents
- Introduction to CNC Machine Tools
- Historical Development of CNC Technology
- Current Landscape of CNC Machine Tools
- Technological Advancements Shaping the Future
- The Role of Automation in CNC Machining
- Sustainability in CNC Machining
- CNC Machine Tools and Industry 4.0
- Challenges Facing CNC Machining and Innovative Solutions
- Conclusion
- FAQs about the Future of CNC Machine Tools
Introduction to CNC Machine Tools
CNC (Computer Numerical Control) machine tools have become indispensable in modern manufacturing. These advanced tools automate the machining processes, ensuring higher precision, speed, and efficiency compared to traditional methods. As industries evolve, so too does the technology behind CNC machines, leading to groundbreaking innovations that transform how products are manufactured.
In this article, we will explore the **dynamic future of CNC machine tools**, examining technological advancements, the role of automation, sustainability initiatives, and emerging trends that are reshaping the landscape of manufacturing.
Historical Development of CNC Technology
Understanding the evolution of CNC technology provides insight into its future potential. CNC machining began in the 1940s and 1950s, driven by the need for precision and efficiency in manufacturing. Early machines were cumbersome and limited in capabilities. However, with the advent of digital electronics in the 1960s, CNC machines underwent a significant transformation, allowing for more complex programming and improved accuracy.
The **1970s and 1980s** marked a period of increased adoption as industries recognized the benefits of CNC machining. By the **1990s**, further advancements in software and hardware made CNC machines more accessible and versatile, leading to their widespread implementation across various sectors.
Today, CNC technology continues to evolve, propelled by innovations in computing power, materials science, and artificial intelligence. This evolution sets the stage for the next phase of CNC machine tools, where the boundaries of manufacturing capabilities are pushed even further.
Current Landscape of CNC Machine Tools
The current landscape of CNC machine tools reflects a diverse range of applications and technologies. From milling and turning to laser cutting and plasma cutting, CNC machines offer unparalleled versatility in manufacturing. Industries such as aerospace, automotive, and medical are increasingly relying on CNC machining for complex parts that demand precision and reliability.
Modern CNC machines are equipped with advanced features such as:
- **Multi-axis capabilities**: Allowing for more intricate designs and reduced setup times
- **High-speed machining**: Enabling faster production without sacrificing quality
- **Adaptive machining**: Using real-time data to adjust parameters for optimal performance
With the integration of IoT (Internet of Things) technology, CNC machines can now communicate with other devices, enabling enhanced monitoring and control. This connectivity fosters a more efficient production environment, laying the groundwork for future innovations.
Technological Advancements Shaping the Future
As we look ahead, several technological advancements are poised to redefine CNC machine tools. Here are some key areas of focus:
1. Artificial Intelligence and Machine Learning
AI and machine learning are set to revolutionize CNC machining by enabling predictive maintenance, smarter programming, and improved process optimization. By analyzing vast amounts of data, AI algorithms can identify patterns and predict failures, reducing downtime and maintenance costs.
2. Additive Manufacturing Integration
The integration of additive manufacturing with CNC machining allows for hybrid processes that combine subtractive and additive techniques. This synergy enables the production of complex geometries that were previously impossible with traditional machining methods.
3. Enhanced User Interfaces
User interfaces are becoming more intuitive, making it easier for operators to program and control CNC machines. Touchscreens, gesture controls, and augmented reality are just a few examples of how technology is streamlining the user experience.
4. Advanced Materials
The development of new materials, including composites and advanced alloys, is expanding the capabilities of CNC machining. These materials enable manufacturers to create lighter, stronger, and more durable components that meet the demands of modern industries.
The Role of Automation in CNC Machining
Automation plays a critical role in the future of CNC machine tools. As industries strive for efficiency and cost-effectiveness, the integration of automation technologies is becoming not just beneficial but necessary.
1. Increased Production Rates
Automated CNC machines can run continuously, significantly increasing production rates. This capability allows businesses to meet demand without compromising quality or incurring additional labor costs.
2. Reduced Human Error
Automation minimizes the risk of human error, leading to higher consistency and accuracy in manufacturing. Automated systems can perform repetitive tasks with precision, ensuring that each component meets strict specifications.
3. Flexible Manufacturing Systems
Flexible manufacturing systems (FMS) enable CNC machines to adapt to changing production requirements. By utilizing automated tools and robotics, manufacturers can quickly switch between different products, streamlining operations and reducing lead times.
Sustainability in CNC Machining
As the manufacturing sector faces increasing pressure to adopt sustainable practices, CNC machining is evolving to address these environmental concerns.
1. Energy Efficiency
Modern CNC machines are designed to optimize energy consumption, reducing the carbon footprint of manufacturing processes. Advanced control systems and energy-efficient motors contribute to lower energy use without sacrificing performance.
2. Waste Reduction
CNC machining enables precise material removal, leading to less waste compared to traditional methods. Additionally, recycling and reclaiming materials are becoming standard practices in the industry, further promoting sustainability.
3. Eco-friendly Materials
The use of eco-friendly materials in manufacturing is gaining traction. CNC machining can accommodate various sustainable materials, enabling manufacturers to produce components with a reduced environmental impact.
CNC Machine Tools and Industry 4.0
The rise of Industry 4.0 signifies a paradigm shift in manufacturing, characterized by smart factories and interconnected systems. CNC machines are at the forefront of this transformation, integrating seamlessly with digital technologies to enhance productivity and efficiency.
1. Real-time Data Analytics
CNC machines equipped with sensors can collect real-time data, providing insights into production processes. This data allows manufacturers to make informed decisions and optimize operations for maximum efficiency.
2. Remote Monitoring and Control
With the advent of IoT technology, CNC machines can be monitored and controlled remotely. This capability enables manufacturers to oversee operations from anywhere, improving responsiveness to issues and enhancing overall productivity.
3. Smart Supply Chain Integration
CNC machine tools are becoming integral to smart supply chains, allowing for better inventory management and production scheduling. By leveraging data analytics, manufacturers can synchronize their operations with market demands, reducing excess inventory and improving profitability.
Challenges Facing CNC Machining and Innovative Solutions
Despite the advancements in CNC machining, several challenges remain. Addressing these issues is critical for maximizing the potential of CNC technologies.
1. Skills Gap
The rapid evolution of CNC technology has created a skills gap in the workforce. To combat this, manufacturers must invest in training and development programs to ensure that employees are equipped with the necessary skills to operate advanced CNC machines.
2. High Initial Costs
The initial investment in CNC technology can be daunting for smaller manufacturers. However, leasing options and financing solutions can help alleviate these costs, making CNC machining accessible to a broader range of businesses.
3. Security Concerns
As CNC machines become more connected, security risks also increase. Manufacturers must implement robust cybersecurity measures to protect sensitive data and ensure the integrity of their operations.
Conclusion
The future of CNC machine tools is bright, characterized by rapid technological advancements and innovative practices that promise to transform the manufacturing landscape. From AI integration and automation to sustainability initiatives, these developments will enhance productivity, reduce costs, and improve the overall efficiency of manufacturing processes.
As industries continue to embrace these innovations, we can anticipate a future where CNC machines play an even more pivotal role in driving growth and enhancing competitiveness in the global market. The journey toward a more sophisticated manufacturing environment is just beginning, and businesses that adapt and invest in these technologies will thrive in the years to come.
FAQs about the Future of CNC Machine Tools
1. What are CNC machine tools?
CNC machine tools are automated devices that use computer programming to control the movement and operation of machinery for manufacturing components with high precision.
2. How is AI changing CNC machining?
AI enhances CNC machining by enabling predictive maintenance, optimizing machining processes, and improving programming through data analysis.
3. What role does automation play in manufacturing?
Automation increases production rates, reduces human error, and allows for greater flexibility in manufacturing processes by enabling machines to operate continuously with minimal human intervention.
4. How can CNC machining be more sustainable?
CNC machining can be more sustainable through energy-efficient designs, waste reduction practices, and the use of eco-friendly materials in the manufacturing processes.
5. What challenges do manufacturers face with CNC technology?
Manufacturers face challenges such as a skills gap in the workforce, high initial investment costs, and cybersecurity risks that need to be addressed to maximize the benefits of CNC technology.
- All
- Product Management
- News
- Introduction
- Enterprise outlets
- FAQ
- Enterprise Video
- Enterprise Atlas
Recent information
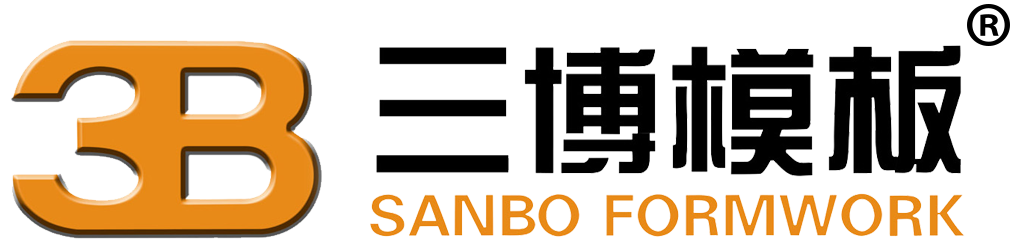
Sanbo specializes in producing high-speed railway, highway bridge formwork, hanging basket formwork, tunnel lining trolley, integral prefabricated formwork, prefabricated segmental assembly formwork system, mobile formwork bridge building machine and water conservancy engineering machinery.
- All
- Product Management
- News
- Introduction
- Enterprise outlets
- FAQ
- Enterprise Video
- Enterprise Atlas